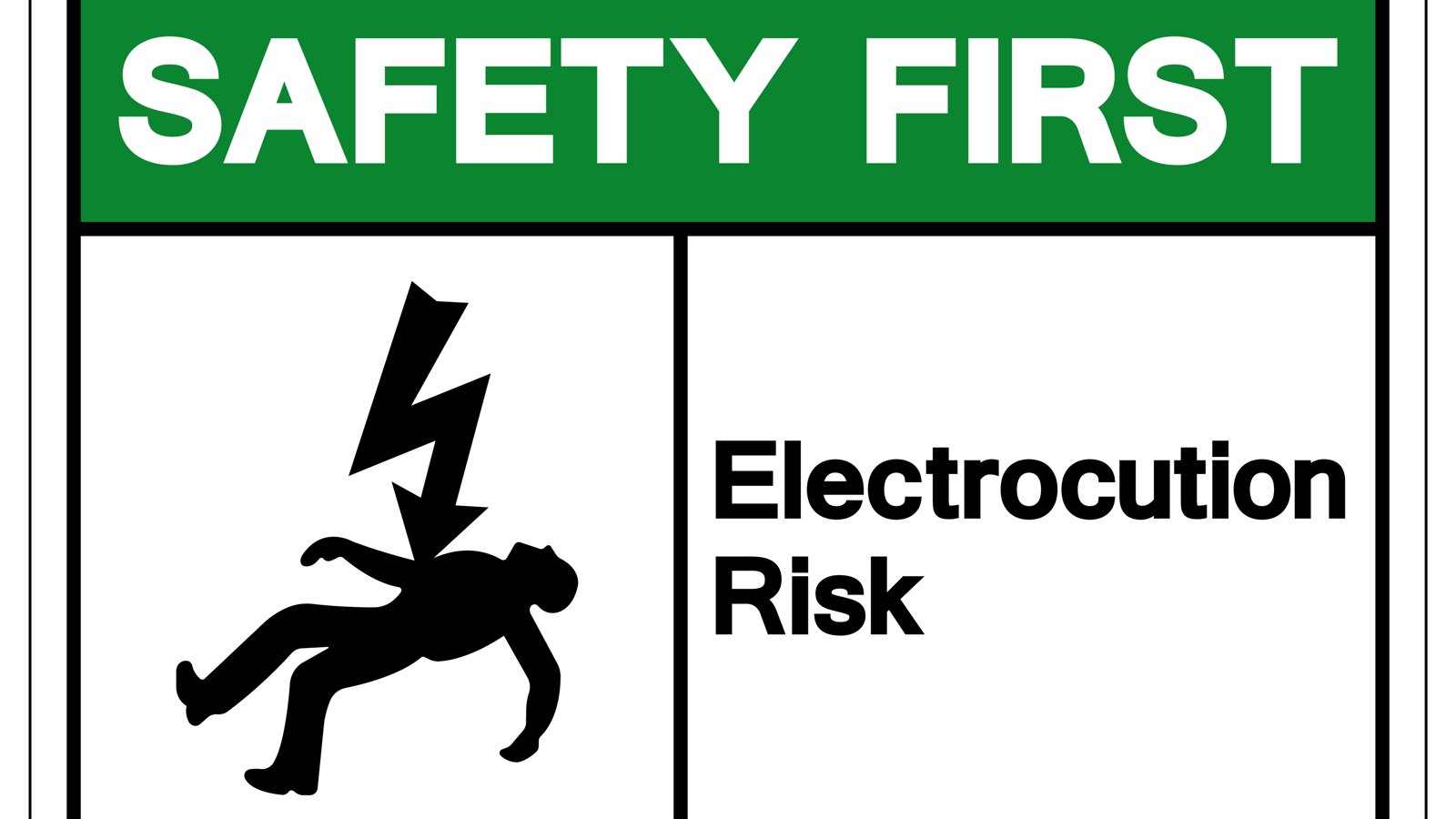
Avoid the risk of electrocution
Today, 90% of goods are transported by sea, and shipping demand is expected to triple its current volume by 2050. The global ship repairing market is growing in tandem, reaching USD 32.29 billion in 2021 and forecasted to soar above USD 39 billion by 2025.
Given these rising demands for ship repair, welding safely under pressure keeps your operations smooth and disruption-free. As the unsung heroes that keep the wheels of our global supply chain turning, keeping our maritime welders safe should be a top priority on board.
The good news is that electrocution injuries are completely avoidable with the right safety precautions. Let’s look at some common mistakes that heighten electrocution risk, and how welders can take steps to stay safe.
What causes electrocution risk in maritime welding?
Working in wet conditions
Our skin usually insulates us from electric shock. But when damp, its resistance is lowered and allows higher current flow through the body. In a wet environment, the current produced by an arc welding machine with 50V DC and above is enough to be lethal.
Damaged welding equipment
Another common cause of shock injuries is worn or damaged equipment, particularly burned out or missing insulators. Using welding machines beyond their ampere or duty cycle ratings can result in overheating.
This can happen when welding is done with short leads or low arc voltages, causing actual welding currents to run higher than indicated on the machines. Because of this, the insulation deteriorates over time and fails to protect against electrical shocks.
Substandard welding machines
Even if your equipment is not worn or damaged, substandard welding machines can increase electrocution risk. When purchasing a welding machine, a critical selection criteria is if the open circuit voltage (OCV) conforms to the maximum safe limit of 25 VAC or 70 VDC, set by the Code of Safe Working Practices for Merchant Seafarers (COSWP).
Using welding machines with non-compliant OCV or without a Voltage Reduction Device will increase the risk of an electrick shock or electrocution.
Improper grounding practices
Grounding is key to electrical safety, and incorrect grounding practices can endanger welders. One common mistake is that the welder uses the ship hull as a return, by clamping the return clamp to the hull.
To prevent current leakage, welders should instead connect the return clamp as close as possible to the workpiece. Wearing personal protective equipment is a must as well.
Reducing electrocution risk with a welding safety checklist
Recalling every little detail of welding safety can be tough. The simplest way to keep safety top-of-mind is a checklist of best practices.
Here is an overview of our recommended precautions on your safety checklist:
Checklist for welding safety |
✓ |
Ensure all electrical supplies, including the earth-leakage circuit breaker (ELCB), are in good condition |
|
Only purchase approved and compliant welding machines for maritime environment use, with a minimum Ingress Protection of IP 23S, a voltage reduction device (VRD), and only use DC welding power sources with an OCVmax of below 70 volts DC |
|
Conduct checks on welding machines and accessories, and repair any damaged parts before use |
|
Avoid working in a wet environment as even sweat can lower your body’s resistance to electrical shock |
|
Wear dry and insulated protective clothing |
|
Use rubber-soled shoes or stand on an insulated mat to protect yourself from the work piece and return cable |
|
Use fully insulated electrode holders and welding cables, and avoid damaged, undersized, or poorly spliced cables |
|
Do not wrap cables that are carrying current around your body |
|
Avoid handling an energized electrode with your bare hands or touching return cables. After welding, ensure the stick electrode is removed from the electrode holder. |
|
Service, maintain, and inspect welding machines and accessories regularly |
|
Staying safe with the right equipment
Ultimately, welding safety starts from within. While this safety checklist serves as a reminder, your crew should be trained to stay mindful of electric shock or electrocution risks at all times and know how to manage a hazardous situation.
Electrical accidents might be an ever-present threat for welders—but at Wilhelmsen, we believe they are also completely preventable. With the right safety awareness and equipment, you can minimise electrocution risk while maximising your crew’s effectiveness.
More information on our welding safety inspection (WSI) service, visit here.
Subscribe to WSS YouTube channel for more video content on welding safety. Subscribe now