


Last updated: 30/04/2025 05:18:52
UNITOR CATALYTIC FINES TEST KIT
Product Code
- Product group:
- 663
- Product number:
- 735748
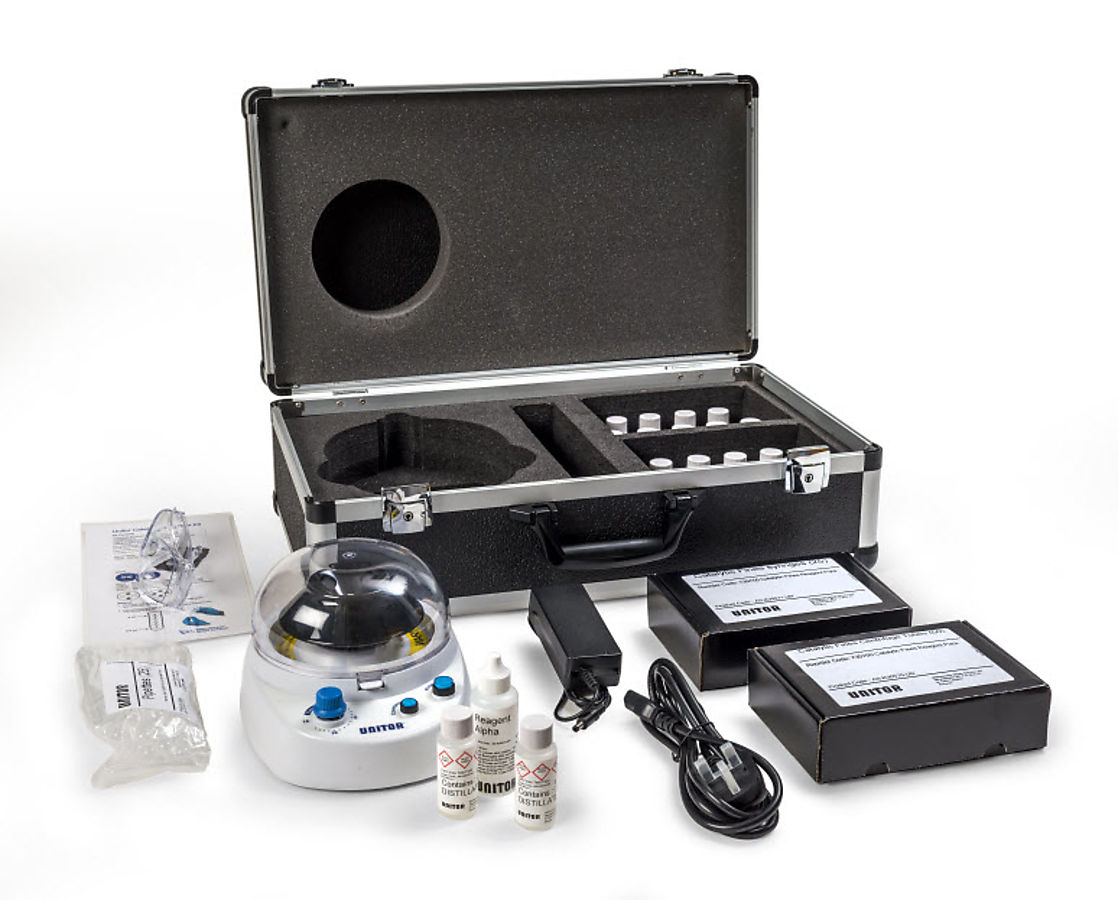
Much of the heavy fuel oil (HFO), burnt in the cylinders of large 2-stroke marine diesel engines, is contaminated with hard particles known as catalytic (cat) fines. These particles, which find their way into the fuel at the oil refinery, can cause catastrophic abrasive damage to engine cylinder liners during the combustion process. This problem has been inadvertently exacerbated by recent changes to the regulation of marine air pollution because it has driven the use of cat-fine prone, low-sulphur fuel oils. As a means of self-preservation, vessels collect representative fuel samples during bunkering and then send them off for laboratory analysis. However, the test results often only become available once a ship has set sail and is far out to sea, by which time significant engine damage may already be in progress. Testing with Unitor Catalytic Fines Test Kit protects your engine from unwanted catalytic fines wear from VLSFO introduced through IMO 2020. An easy to use test kit used to measure the catalytic fines in fuel oil. The test kit will flag fuel samples with dangerous levels of catalytic fines.